A la hora de plantear un depósito, una de las cuestiones más importantes es ver qué tipo de solución es la más adecuada para obtener el mejor ratio de capacidad física. De todas formas, debemos también tener en cuenta que esta no es la única característica que nos debe interesar ya que hay otros factores igualmente esenciales que determinarán si nuestra instalación es efectiva o no como, por ejemplo, la agilidad que se consigue en el manejo de los pallets.
Por otra parte, la capacidad física de un depósito (el número máximo de pallets que se pueden alojar a la vez) no es siempre equivalente a su capacidad efectiva, que no es otra cosa que la que se puede conseguir en un ciclo normal de trabajo según los máximos y mínimos de las referencias y el espacio que se tenga que destinar a cada una de ellas.
En esta cuestión resulta primordial el sistema de ubicación que se emplee puestos que no todos son siempre igual de efectivos:
- El sistema de ubicación específico requiere la reserva de un número determinado de huecos para cada referencia, a excepción de aquellas que pueden compartir ubicaciones con otras. Cuando entra mercadería en el depósito, se procede a llenar todos los huecos disponibles, pero según se preparan los pedidos esas posiciones se quedan vacías y, dado que están reservadas y no se pueden llenar con otras referencias, por lo que la capacidad efectiva será distinta a la física. En concreto, la capacidad efectiva será la del stock mínimo, más la mitad de la diferencia entre dicho stock mínimo y el número de huecos asignados a esa referencia. La capacidad efectiva de estos sistemas de ubicación específica se sitúa entre el 55 y el 65% de la real.
- Si se trabaja con una ubicación caótica, el sistema de gestión se encarga de asignar las posiciones de los pallets, que se introducirán aleatoriamente en cualquier hueco vacío, y será el SGA el que se encargue de registrar la ubicación y de informar al operario cuando sea necesario. En este caso, no hay huecos vacíos, prácticamente, por lo que la capacidad real y la física será muy similar, entre un 80 y un 92%.
De no tener en cuenta estas diferencias, la solución escogida para el depósito puede no ser la correcta. Cualquier sistema puede funcionar con los dos tipos de ubicación mencionados, pero, por ejemplo, los sistemas de almacenaje por compactación no son flexibles y puede darse que aunque tengan más capacidad física que otros sistemas, es posible que su capacidad efectiva sea menor.
Ejemplos prácticos
Para ilustrar las diferencias que pueden surgir en las instalaciones a la hora de utilizar un sistema u otro de almacenaje, se expone a continuación un caso hipotético de un depósito con unas medidas determinadas y una unidad de carga concreta. Sobre este caso, se ofrecen distintas soluciones (configuraciones y equipos de manutención) y se especifican los resultados al emplear una u otra.
La capacidad se calcula en función de la superficie y se define a partir de un nivel de almacenaje, ya que la altura es una variable que depende del propio edificio y de la elevación que puede alcanzar el autoelevador. Para facilitar la comparación, tampoco se ha tenido en cuenta el espacio necesario para las zonas de recepción y expedición. La unidad de carga elegida es un pallet de 1.200 x 800 mm (europallet), lo que en el sistema de paletización convencional significa que se pueden almacenar hasta tres de estos pallets por cada hueco de 2.700 mm de anchura.
La capacidad (y, por lo tanto, el ratio de ocupación) está especificada por nivel, es decir, por superficie, no por volumen total de la instalación.
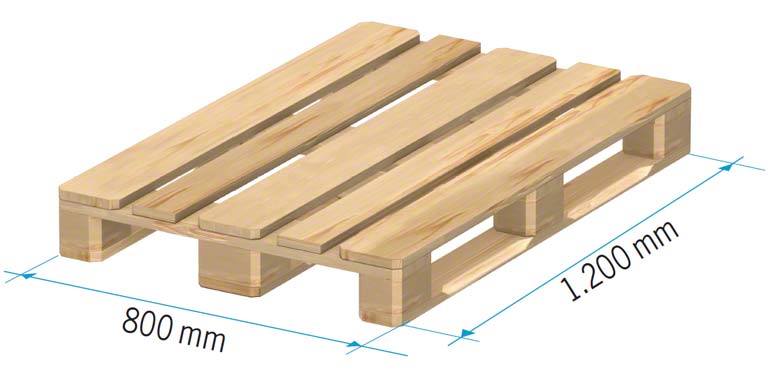
Unidad de carga: pallet de 1.200 x 800 mm.
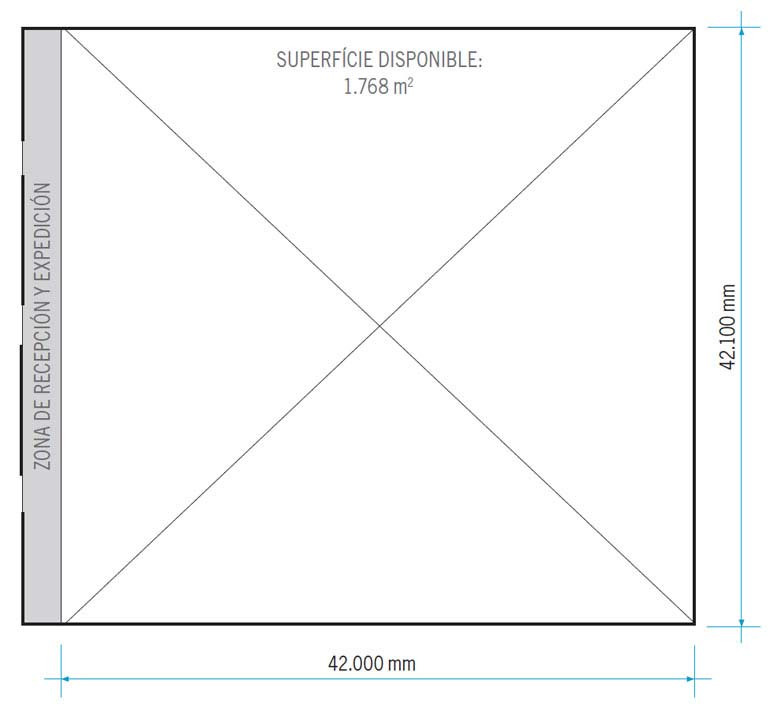
Ejemplo 1. Paletización convencional con autoelevador contrapesado. 594 pallets por nivel |
Sistema: Paletización convencional Pasillo: 3.500 mm. Como mínimo 3.600 mm entre estanterías Manutención: Autoelevador eléctrico contrapesado Capacidad obtenida: 594 pallets por nivel |
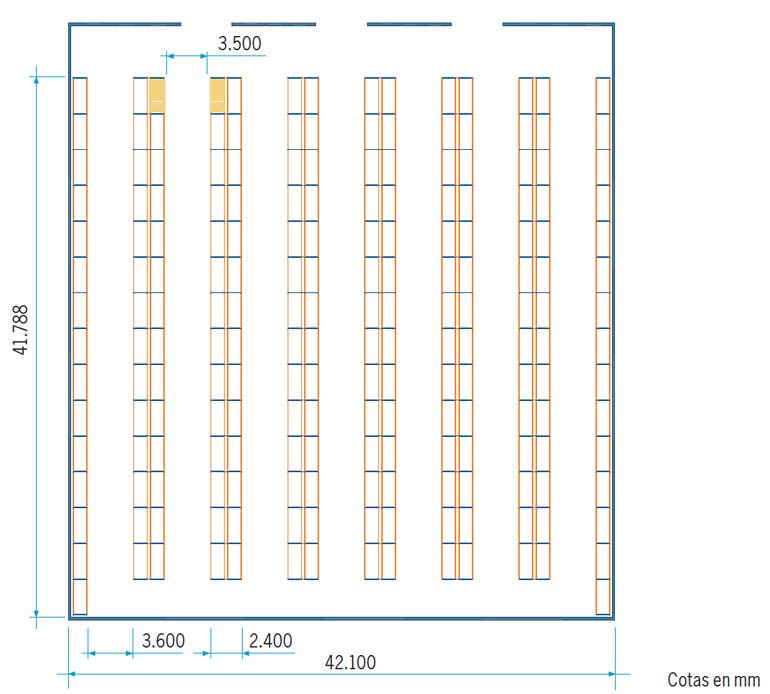
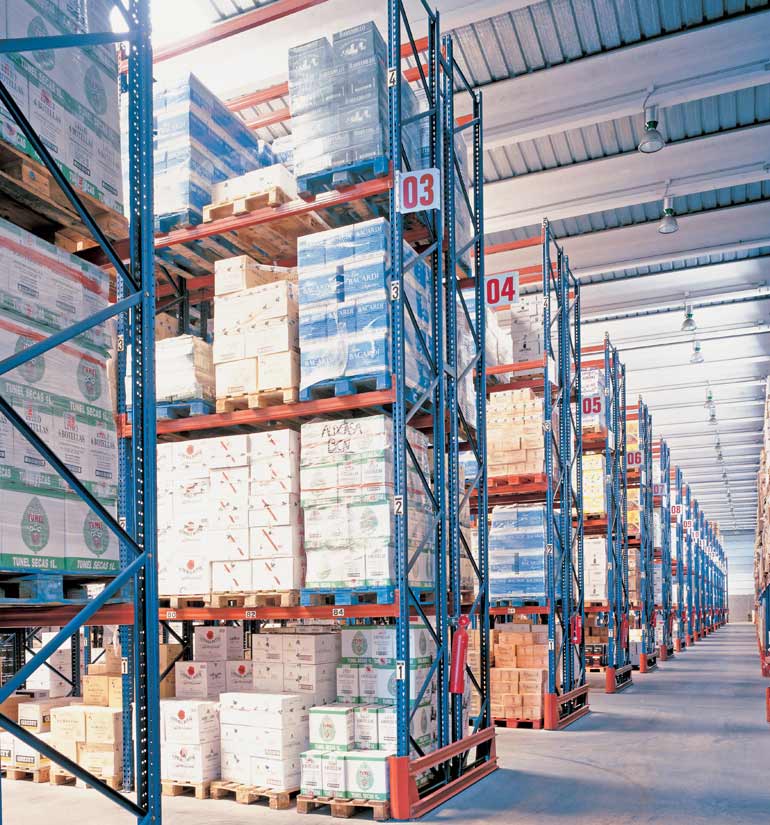
Depósito para una empresa de distribución
Ejemplo 2. Paletización convencional con autoelevador retráctil. 678 pallets por nivel |
Sistema: Paletización convencional Manutención: Autoelevador retráctil Pasillo: 2.750 mm. Como mínimo, 2.850 mm entre estanterías Capacidad obtenida: 678 pallets por nivel |
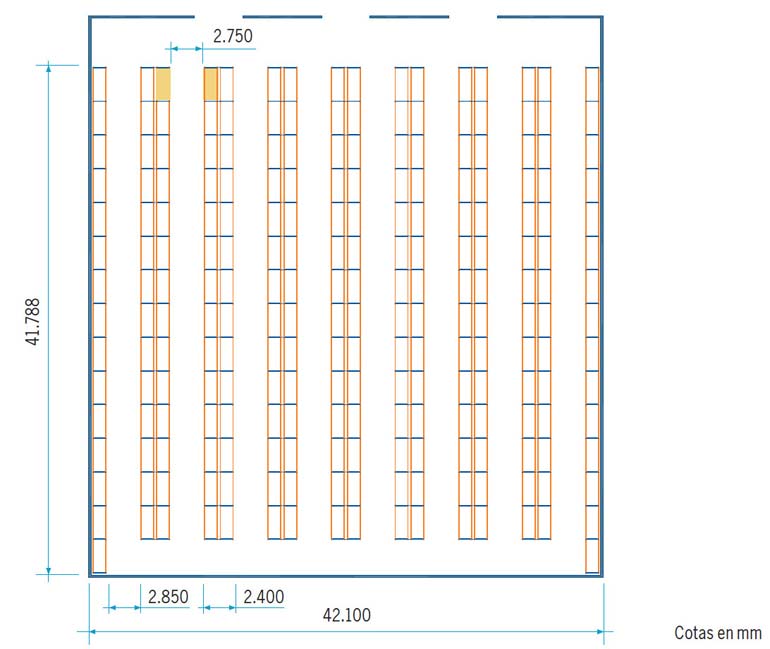
Depósito de un operador logístico
Ejemplo 3. Paletización convencional con autoelevador tipo torre trilateral o con transelevador. 840 pallets por nivel |
Sistema: Paletización convencional Manutención: Autoelevador tipo torre trilateral o transelevador Pasillo: 1.700 mm. Como mínimo, 1.800 mm entre estanterías Capacidad obtenida: 840 pallets por nivel Nota: Un transelevador puede trabajar en un pasillo de 1.500 mm entre cargas, por lo que la anchura del espacio disponible del ejemplo puede ser de 40.000 mm, en lugar de 42.100 mm, para obtener el mismo resultado |
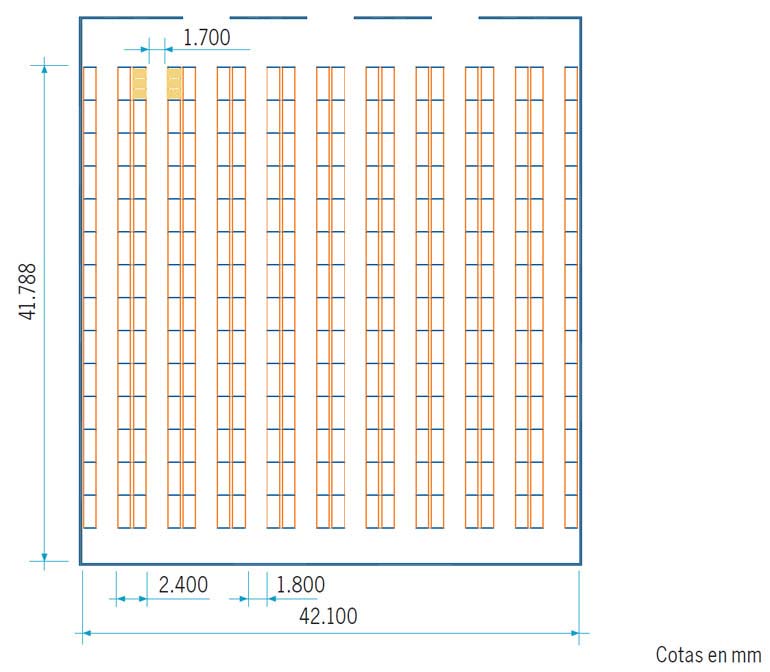
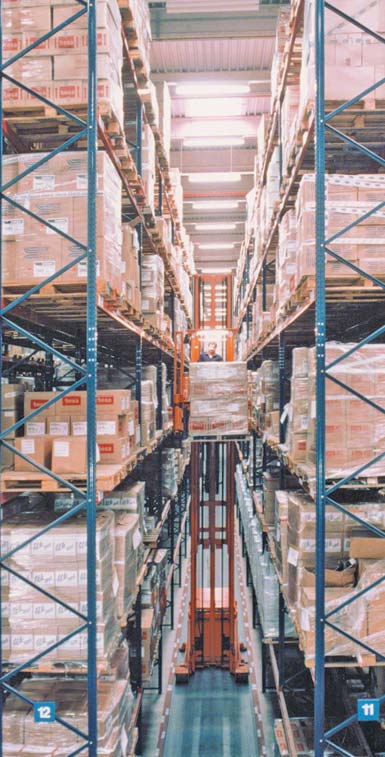
Depósito trilateral
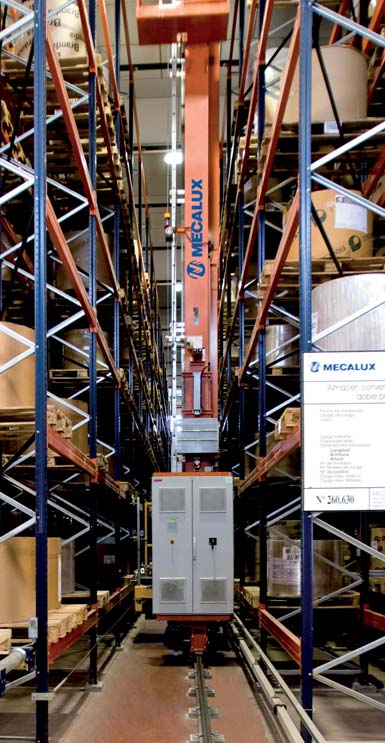
Depósito automático de bobinas de papel
Ejemplo.4. Paletización convencional de doble profundidad con transelevador. 1.008 pallets por nivel |
Sistema: Paletización convencional de doble profundidad Manutención: Transelevador Pasillo: 1.500 mm como mínimo, 1.600 mm entre estanterías Capacidad obtenida: 1.008 palets por nivel Nota: Al igual que en el Ejemplo 3, para esta instalación el depósito puede medir 40.000 mm de ancho en vez de 42.000 mm. |
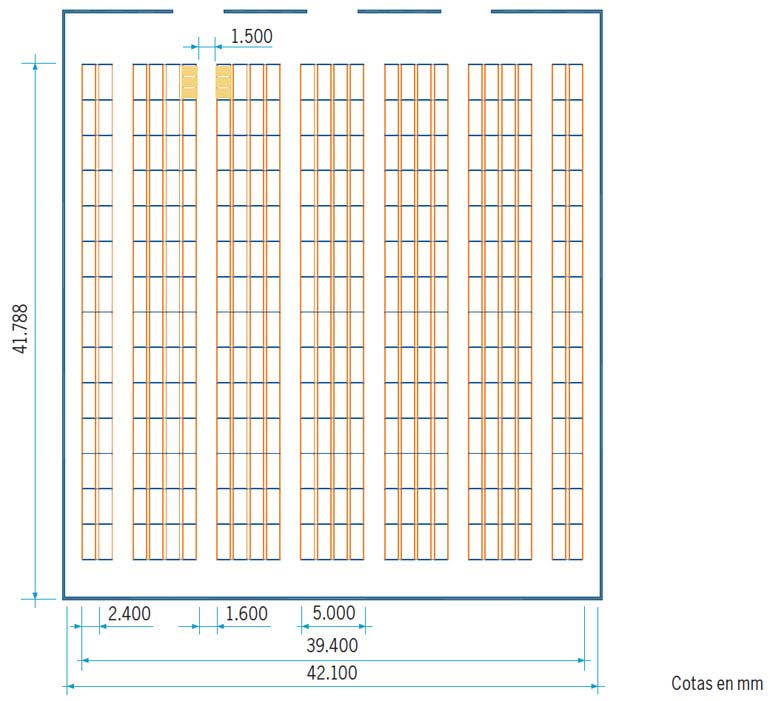
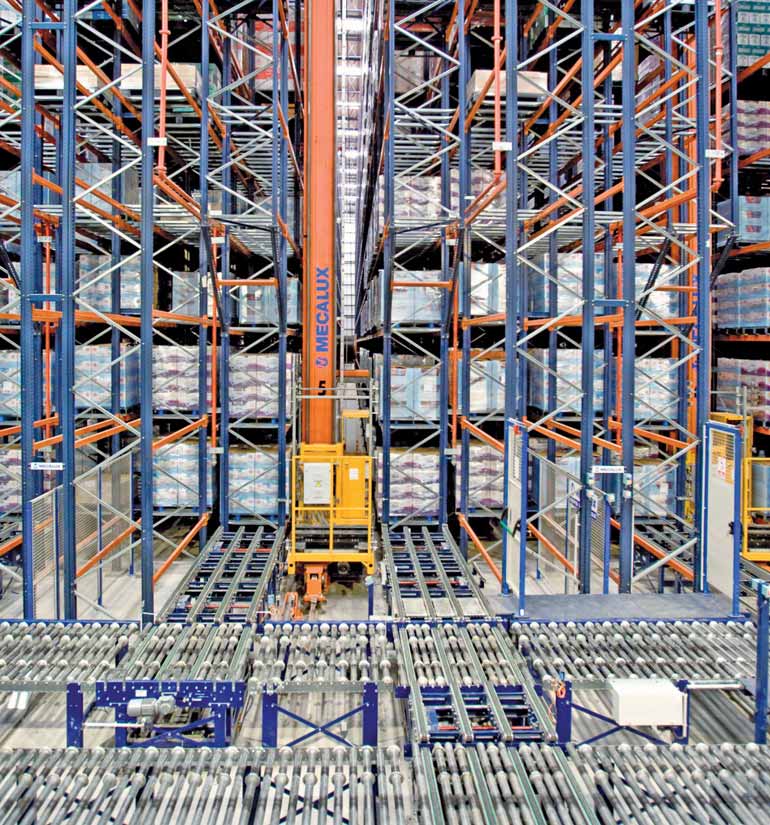
Depósito de productos de gran consumo
Ejemplo 5. Paletización convencional sobre bases móviles. 1.144 palets por nivel |
Sistema: Paletización convencional sobre bases móviles Manutención: Autoelevadores Pasillos: Dos de 3.750 mm cada uno. En ellos se pueden cruzar dos autoelevadores (respetando los márgenes adecuados) Capacidad obtenida: 1.144 pallets por nivel |
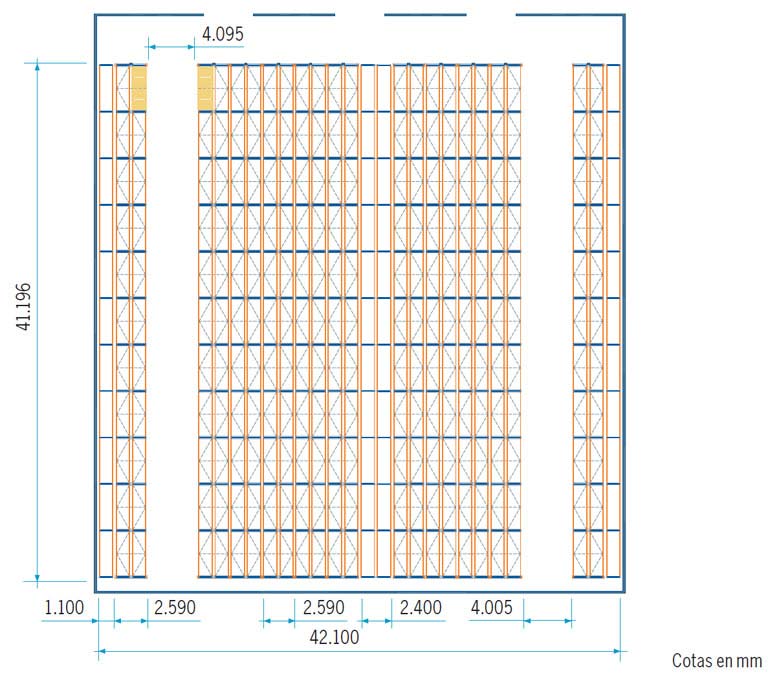
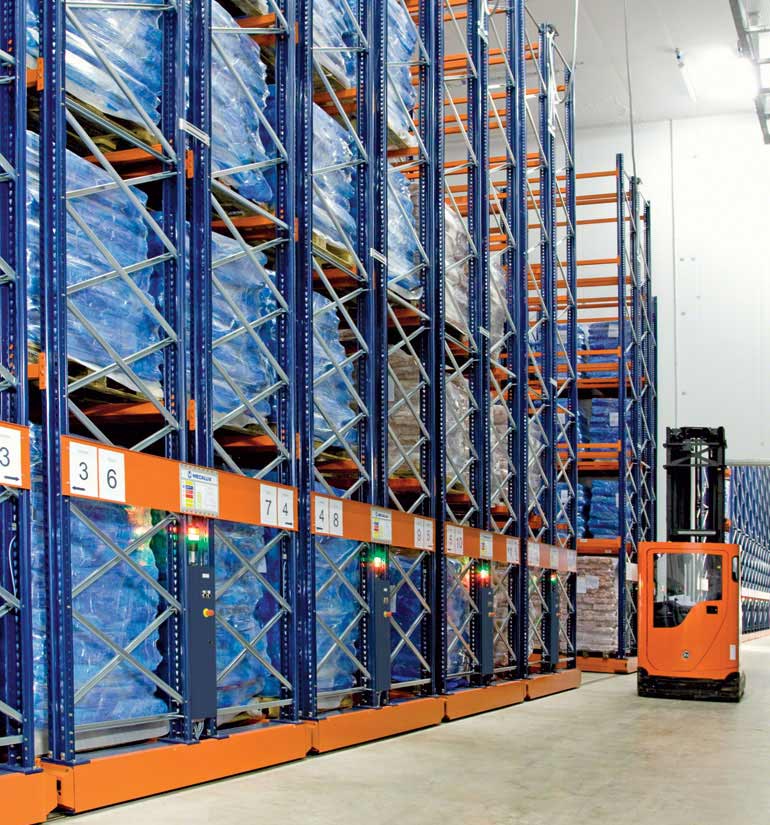
Depósito de carne congelada
Ejemplo 6. Paletización compacta. 960 palets por nivel |
Sistema: Paletización compacta Manutención: autolevadores Pasillo: 3.500 mm, con capacidad para cruzarse dos autoelevadores Capacidad obtenida: 960 pallets por nivel |
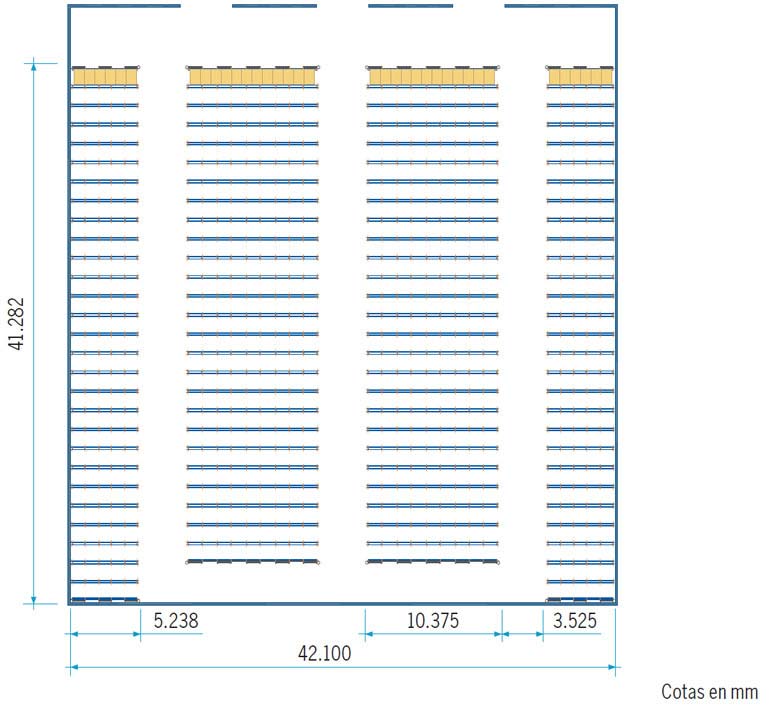
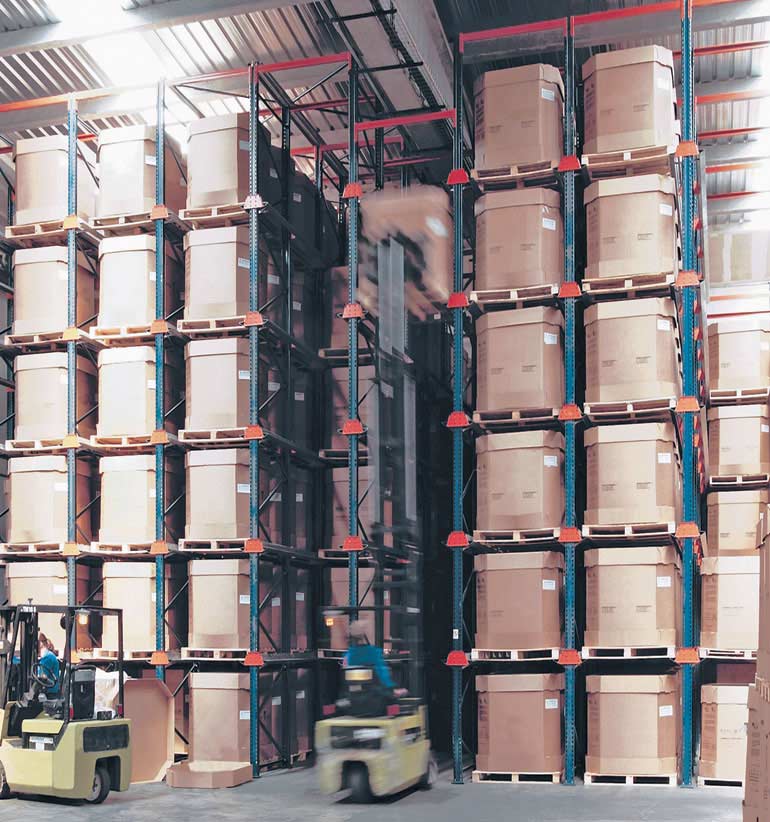
Ejemplo 7. Push-back de carros. 848 pallets por nivel |
Sistema: Push-back de carros Manutención: Autoelevadores Pasillo: 3.500 mm, como mínimo Capacidad obtenida: 848 pallets por nivel |
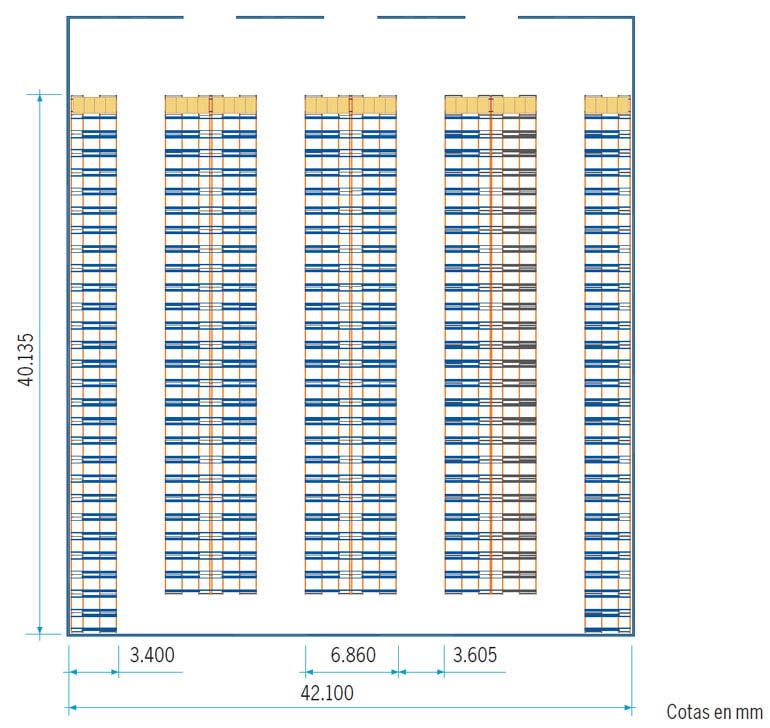
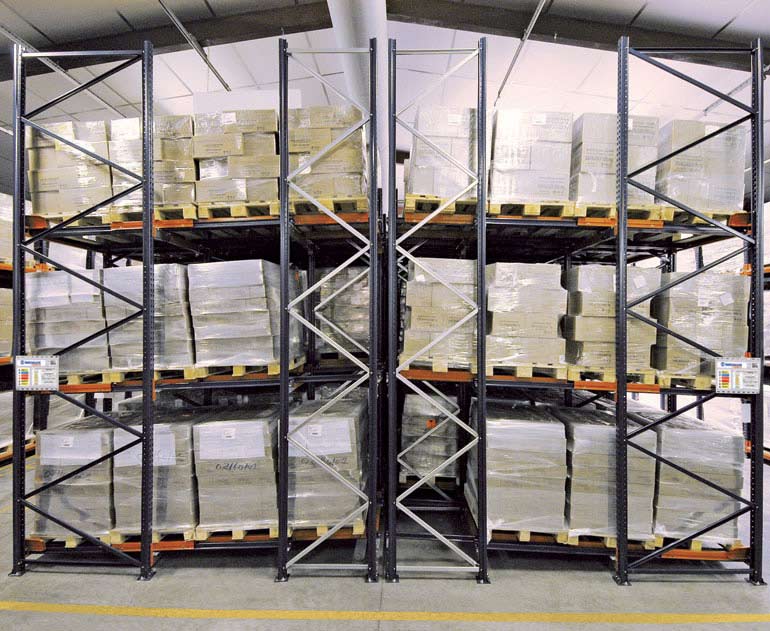
Ejemplo 8. Push-back de rodillos, 893 pallets por nivel |
Sistema: Push-back de rodillos Manutención: Autoelevadores Pasillo: 3.400 mm, como mínimo Capacidad obtenida: 893 pallets por nivel |

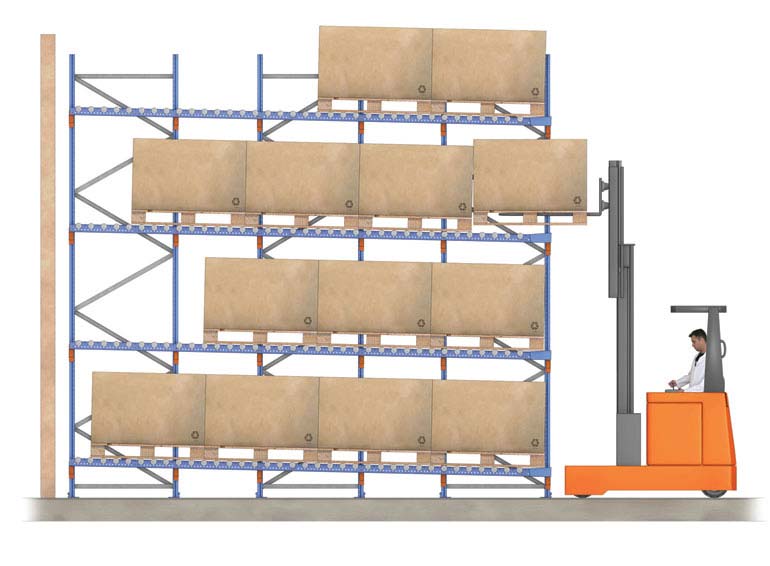
Ejemplo 9. Paletización con Pallet Shuttle. 1.080 pallets por nivel |
Sistema: Paletización con Pallet Shuttle Manutención: Autoelevadores Pasillo: 3.500 mm, como mínimo (paso para dos autoelevadores) Capacidad obtenida: 1.080 pallets por nivel |

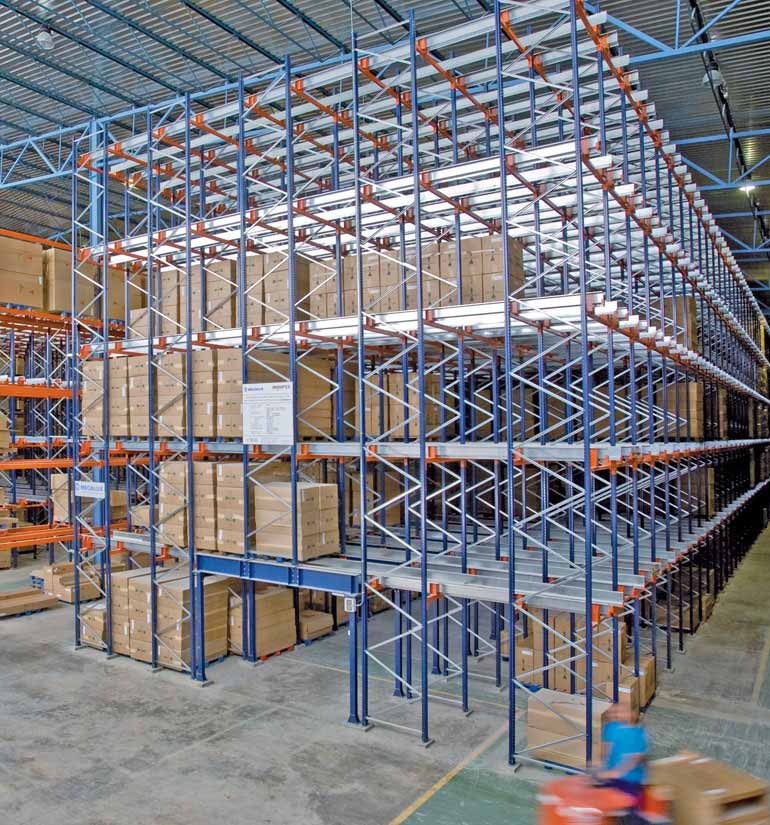
Empresa de muebles en kits
Ejemplo 10. Estanteria dinámica de palets. 910 pallets por nivel |
Sistema: Estanterías dinámicas de pallets Manutención: Autoelevadores Pasillo: 3.400 mm como mínimo Capacidad obtenida: 910 pallets por nivel |
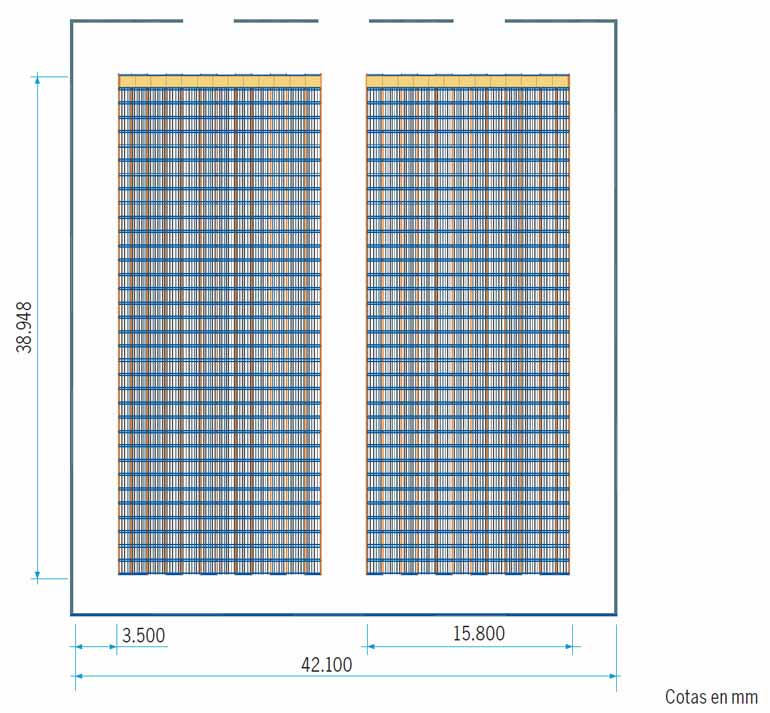
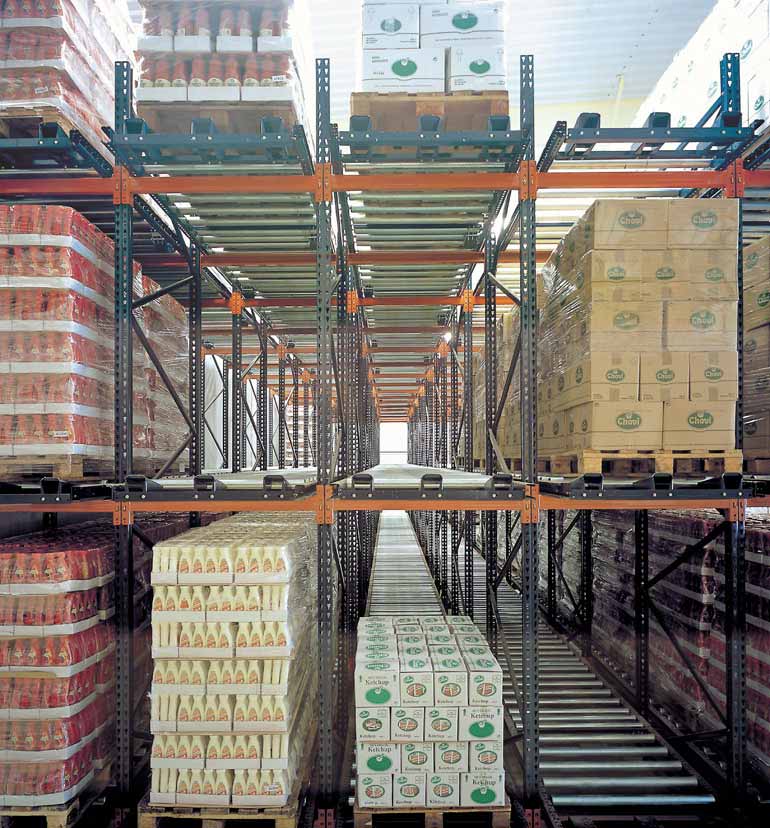
Empresa fabricante de jugos
Tabla resumen comparativa de la capacidad física |
|||
Sistema de almacenaje | Pallets por nivel | Superficie para pallets | Ratio (proporción del local ocupada por pallets) |
Depósito convencional con autoelevador contrapesado | 594 | 570 m2 | 32,2 % |
Depósito convencional con autoelevador retráctil | 678 | 651 m2 | 39,2 % |
Depósito convencional con autoelevador torre trilateral o transelevador | 840 | 806 m2 | 45,7 % |
Depósito convencional de doble fondo servido por transelevador | 1.008 | 968 m2 | 54,9% |
Depósito convencional con bases móviles | 1.144 | 1.098 m2 | 62,2 % |
Depósito compacto con autoelevador retráctil | 960 | 922 m2 | 53,8 % |
Push-back de carros | 848 | 814 m2 | 46,0 % |
Push-back de rodillos | 893 | 857 m2 | 48,0 % |
Paletización con Pallet-Shuttle | 1.080 | 1.037 m2 | 58,8 % |
Estantería dinámica | 910 | 874 m2 | 47,6 % |
La capacidad por volumen no es lineal ya que influyen otros factores, como la altura útil del depósito y la optimización en la altura de los pallets. Otro factor determinante es el sistema constructivo, ya que en las estanterías dinámicas se produce una pérdida de altura por la pendiente que este sistema utiliza; en las instalaciones de doble fondo con transelevador es necesaria una mayor separación entre niveles, por ejemplo; y en otros casos es preciso contar con perfiles de apoyo y una altura concreta en el primer nivel.
Esta tabla tan solo es válida a modo orientativo y está referida a la capacidad física, no a la efectiva.