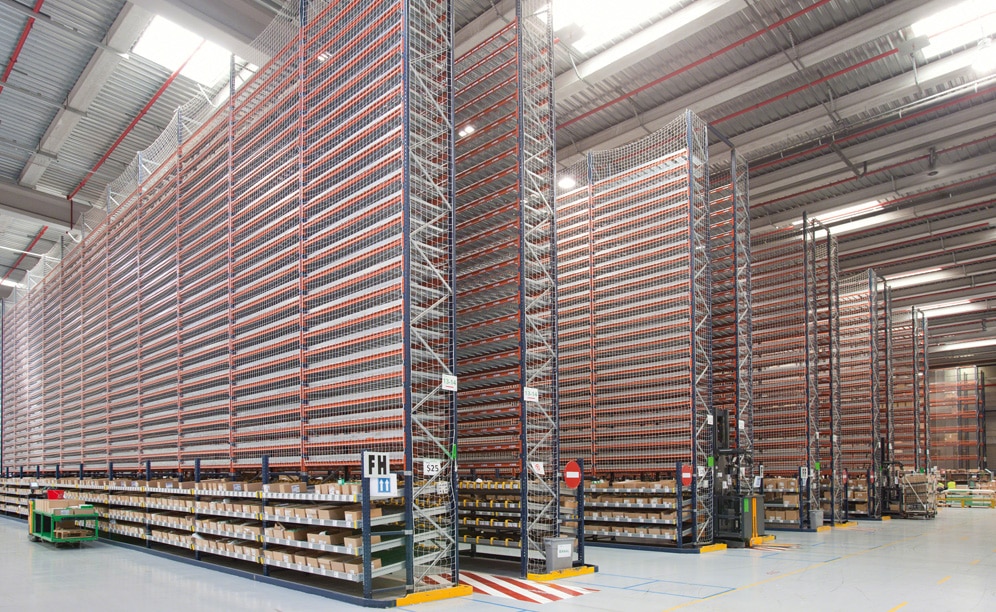
Cómo lograr el equilibrio idóneo entre la agilidad en el picking y la capacidad de almacenaje
La combinación de sistemas para pallets y cajas aumenta la eficiencia logística de Schneider Electric
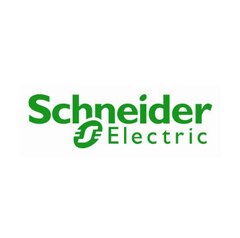
Mecalux ha equipado el nuevo centro logístico de Schneider Electric en Sant Boi de Llobregat (Barcelona) en base a los objetivos planteados por la empresa: conseguir gran agilidad en la preparación de pedidos, así como adaptar los sistemas de almacenaje a su gran variedad de productos y en función del segmento de mercado al cual van destinados.
Referente mundial en el sector eléctrico
Fundada en 1836, Schneider Electric se ha convertido en un referente mundial de tecnologías y soluciones de gestión de la energía, ofreciendo recursos tecnológicos que permiten procesarla de una forma segura, fiable, eficiente y sostenible. Con una larga trayectoria en España, la compañía siempre ha contado con la colaboración de Mecalux a fin de encontrar los mejores sistemas de almacenaje para sus productos.
Necesidad de Schneider Electric
Schneider Electric requería una ampliación de su depósito para poder ubicar la gran variedad de productos que ofrece, desde componentes de reducidas dimensiones hasta complementos para la industria de tamaño voluminoso. El consumo de sus mercaderías es irregular y cumple el principio de Pareto, o regla del 80/20, es decir, el 20% de las referencias generan el 80% de las ventas. Además, el 80% de todas las referencias son de tamaño pequeño y en el depósito se realizan principalmente operaciones de picking, así que un porcentaje importante de los pedidos suelen tener poco volumen y en pocas ocasiones se suministran los pallets completos.
La experiencia de los equipos técnicos y logísticos de Schneider Electric con diferentes soluciones aplicadas en otros de sus depósitos, inclinó a la compañía a instalar sistemas de almacenaje convencionales para pallets y cajas, combinados con sistemas y equipos informáticos avanzados para su óptima gestión.
Solución propuesta por Mecalux
Con todos estos factores a tener en cuenta, Mecalux implementó en un espacio de 22.000 m2 distintos sistemas de almacenaje que se adecuan a las necesidades de Schneider Electric.
El depósito se divide en dos sectores diferentes, cada uno con sus propios muelles de carga y descarga. Esto es así por motivos de seguridad, pero también con el propósito de facilitar la separación de los productos según su tamaño y el segmento de mercado al que van dirigidos. En la gran mayoría de casos, las cajas que contienen los productos, en especial los de pequeñas dimensiones, se almacenan directamente en estantes y no en pallets.
Las soluciones adoptadas para satisfacer los requerimientos de la compañía han favorecido la agilidad en la preparación de los pedidos frente a la capacidad de almacenaje:
- Picking sobre niveles dinámicos de cajas utilizando máquinas preparadoras de pedidos de alta y baja cota.
- Picking sobre estantes de malla mediante preparadoras de pedidos de alta cota.
- Picking sobre niveles dinámicos de pallets, combinando máquinas trilaterales y preparadoras de pedidos de baja cota.
- Picking sobre racks selectivos, con uso de máquinas trilaterales y preparadoras de pedidos de baja cota.
- Picking sobre pallets y estantes mediante autoelevadores retráctiles y preparadoras de pedidos de baja cota.
- Almacenaje de productos voluminosos en racks selectivos empleando autoelevadores retráctiles.
- Almacenaje de perfiles de grandes dimensiones en estanterías cantilever con la ayuda de autoelevadores retráctiles.
- Embalaje y consolidación en una entreplanta de grandes luces.
Los productos de mayor consumo
Schneider Electric necesitaba una solución óptima para los productos de mayor consumo (tipo A y B) de pequeñas dimensiones. Por eso se instalaron estanterías con canales dinámicos en sus niveles inferiores donde realizar directamente las tareas de picking. Los niveles superiores están destinados a depositar las cajas de reserva.
Se han dispuesto pasillos de trabajo con suficiente amplitud para permitir que distintos operarios puedan trabajar a la vez con gran agilidad y evitando interferencias. Preparan los pedidos y los agrupan en olas con la ayuda de terminales de radiofrecuencia, que facilitan la identificación y clasificación de los productos.
Estos estantes se alimentan desde pasillos más estrechos donde circulan máquinas preparadoras de pedidos de gran altura, que se utilizan para reponer las cajas de reserva y alojarlas en los niveles superiores. Esta solución aporta las siguientes ventajas:
- Siempre hay producto disponible. En los canales se acumulan varias cajas en profundidad de una misma referencia y van avanzando sus posiciones a medida que se van retirando las primeras.
- Permite una gran diversidad de productos, ya que cada canal puede almacenar una referencia distinta.
- No hay interferencias en las labores de preparación de picking y reposición, puesto que las tareas se llevan a cabo en pasillos diferentes.
- Posibilita un máximo aprovechamiento de la altura.
- Mayor rendimiento de los operarios gracias a la ergonomía de las posiciones de trabajo, que facilita la manipulación de los productos.
Los productos de menor consumo
Las cajas con referencias de menor consumo y de pequeñas dimensiones se colocan en estanterías de gran altura. Los pasillos son muy angostos y se emplean máquinas preparadoras de pedidos en altura y carros con posiciones multipedidos, logrando así una buena accesibilidad y una elevada capacidad.
Estas máquinas se usan también para reponer los productos, pero en unas franjas horarias distintas. Con el fin de facilitar este proceso, se ha dispuesto un espacio de parking de carros con productos preparados para reponer.
Este sistema de almacenaje es complementario al de productos tipo A y B de pequeñas dimensiones citados anteriormente, ya que en ambos casos se prepara el mismo tipo de productos pero con una rotación diferente.
Para finalizar el proceso, los pedidos preparados en ambas zonas se consolidan en una entreplanta situada en un área próxima y junto a los muelles utilizando transportadores de rodillos y de bandas.
Referencias paletizadas
Las referencias de mayor tamaño se depositan en pallets como unidad de transporte y almacenaje, con dimensiones que pueden variar en función del volumen de los productos. Los pallets son de 1.200 x 800 mm y de 600 x 800 mm. En esta área se han instalado diferentes composiciones de estanterías de paletización.
Por su parte, los productos de dimensiones medianas y de mayor consumo se almacenan en estanterías de simple acceso, con niveles formados por estantes perforados que permiten colocar pallets de diferentes medidas. En esta zona se utilizan máquinas elevadoras trilaterales para realizar las tareas de reposición, por lo que los pasillos son más angostos. Estos pasillos no interfieren con los pasillos más anchos donde se hace picking mediante preparadoras de pedidos de baja cota.
Las tareas de picking tienen lugar en el nivel inferior de las estanterías. Un operario sitúa los pallets con las reservas en los estantes superiores mediante una máquina trilateral. Posteriormente, repone el producto en los niveles inferiores, bajando el pallet correspondiente desde su ubicación.
Los productos voluminosos
Los demás productos paletizados se almacenan en racks selectivos alimentadas mediante autoelevadores retráctiles. El criterio de ubicación de los diferentes pallets se basa en las dimensiones de las referencias. En estas estanterías se pueden depositar pallets de 1.200 x 800 mm o de medias superiores, disponiendo de uno, dos o tres pallets por hueco según su tamaño. La preparación de pedidos se lleva a cabo en el mismo pasillo donde circula el autoelevador.
Los productos de grandes dimensiones y también los de gran longitud se colocan en estanterías cantilever y se manipulan empleando el mismo tipo de autoelevadores de manutención.
La entreplanta como área de consolidación
La solución escogida para el área de preparación y consolidación de los pedidos de pequeñas dimensiones es una entreplanta de grandes luces con perfiles estructurales laminados en caliente. Este sistema ha aportado a Schneider ciertas ventajas:
- Obtener espacios amplios y diáfanos en la parte inferior, al tratarse de una estructura que necesita un número de columnas reducido.
- Poder proteger la estructura mediante pintura intumescente con alta resistencia al fuego, lo cual no es posible con perfiles laminados en frío.
- Facilitar el desmontaje y la transformación del sistema.
El piso de la entreplanta es de madera tratada con acabado en melamina blanca por la parte inferior y melamina rugosa de color gris oscuro con alta resistencia a la abrasión en la parte superior. Es un acabado antideslizante y, además, permite el paso de carros y transpallets manteniendo sus características mecánicas durante un largo tiempo.
Los autoelevadores manipulan los pallets desde el suelo. En uno de los laterales del nivel superior de la entreplanta, se han dispuesto dos puertas o barandillas basculantes para la seguridad de los operarios.
Áreas de consolidación y expedición
En este depósito se preparan los pedidos por áreas en función del tipo de referencias, por lo que ha sido necesario habilitar en cada una de ellas una zona específica para su consolidación, con los equipos necesarios de embalaje y etiquetaje. Hay tres áreas distintas:
- Los perfiles y productos voluminosos se consolidan en los espacios cercanos a los muelles de carga.
- Los productos de dimensiones medianas se colocan en una amplia zona en el suelo.
- Para las referencias de pequeñas dimensiones –dado que suponen el grueso más importante de pedidos–, se ha reservado un espacio cercano a la entreplanta y los dos niveles que la componen.
Dada su importancia, esta última zona de consolidación se ha organizado en torno a los siguientes elementos:
- Espacio para aparcar provisionalmente los carros con pedidos una vez preparados.
- Transportadores de bandas para desplazar las cajas entre los dos niveles de la entreplanta.
- Clasificadores automáticos para los pedidos en fase de consolidación.
- Transportadores y clasificadores para los pedidos finalizados.
- Mesas para la consolidación.
- Flejadoras y equipos auxiliares para el empaquetado de la mercadería.
- Equipos informáticos de control, identificación e impresión de etiquetas y packing list.
En la parte superior de la entreplanta, se preparan los pedidos en cajas de envío. Así, la parte inferior se dedica a la preparación de los pallets según un criterio de clasificación por rutas. Posteriormente, se trasladan a las zonas de precargas, que coinciden con los muelles asignados.
Beneficios para Schneider Electric
- Maximización del almacenaje: el nuevo depósito de 22.000 m2 de Schneider Electric está equipado con distintos sistemas de almacenamiento que se adaptan a su amplia variedad de productos, con dimensiones muy distintas.
- Ágil sistema de preparación de pedidos: se ha instalado el sistema de preparación de pedidos más idóneo en función del tamaño de los productos y el segmento de mercado al que van dirigidos.
- Alta productividad: la combinación de las funciones de picking en los niveles inferiores de las estanterías y la reserva de mercadería en la parte superior aporta una gran eficiencia, aumentando la velocidad en la preparación de pedidos.
Galería
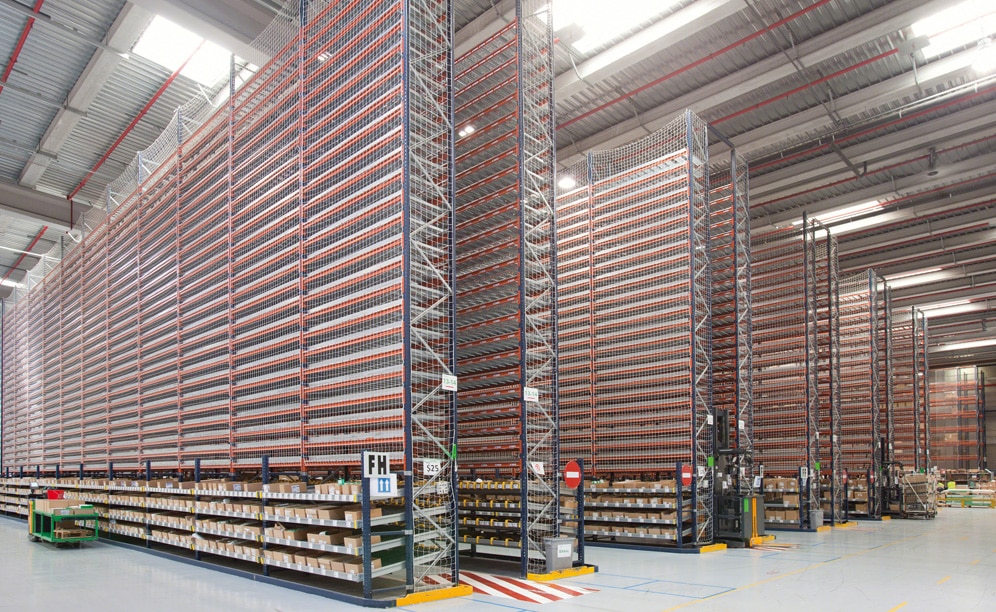
El nuevo depósito de 22.000 m² de Schneider Electric está equipado con distintos sistemas de almacenamiento que se adaptan a su amplia variedad de productos
Consulte con un experto