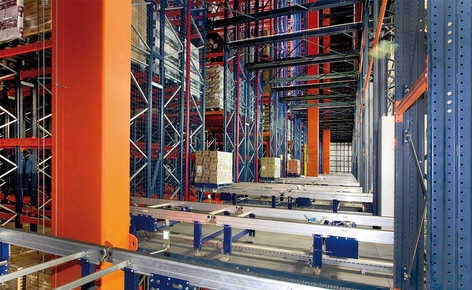
Grupo Siro ha multiplicado su capacidad y productividad con un depósito automático autoportante
Grupo Siro sigue creciendo con un gran depósito automático autoportante
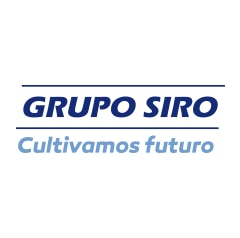
Mecalux ha construido un depósito autoportante de grandes dimensiones completamente automatizado para Grupo Siro, una de las mayores compañías del sector de la alimentación en España. Este innovador centro logístico se enmarca dentro de la apuesta del Grupo por soluciones eficientes a sus necesidades y por las nuevas tecnologías como fuente de eficiencia y crecimiento sostenible.
Quién es Grupo Siro
Grupo Siro es uno de los fabricantes de galletitas, pasta, pan lactal y cereales más importantes de España.
Se constituyó en 1991 con la adquisición de Galletas Siro a Danone y desde entonces siempre ha apostado por la innovación y el uso de la tecnología en todos sus procesos operativos, con el fin de ofrecer productos de la mejor calidad al mejor precio.
Actualmente, fabrica más de 300 productos distintos y cuenta con 13 centros de producción, un depósito logístico, un centro de I+D+i, un centro de valorización de subproducto, dos centros de oficinas y la sede de la Fundación Grupo Siro.
Necesidades del cliente
La empresa ha experimentado un gran crecimiento en los últimos años, debido especialmente a la enorme demanda de su cliente principal: la cadena de supermercados Mercadona.
En cierto momento, este crecimiento y el consecuente aumento de la producción incrementaron las necesidades de espacio de sus depósitos, ubicados generalmente dentro de las propias fábricas. Para mantener el ritmo de producción, la compañía optó en un primer momento por contratar depósitos externos, pero eso dificultaba la coordinación de su cadena logística e incrementaba los costes operativos.
Decidido a apostar por soluciones eficientes a sus necesidades e impulsar su crecimiento, Grupo Siro encargó a Mecalux la construcción de un nuevo centro logístico en su sede central en Venta de Baños (Palencia) con dos premisas muy claras: mejorar la capacidad de almacenaje de sus fábricas y fomentar la eficiencia y productividad de la empresa.
La solución propuesta
El departamento técnico de Mecalux, en colaboración con el equipo logístico de Grupo Siro, analizó en detalle las necesidades, condicionantes y posibilidades, hasta finalmente hallar la solución idónea: la construcción de un depósito autoportante de 36 m de alto servido por transelevadores y transportadores controlados por el sistema de gestión de depósitos Easy WMS de Mecalux.
El centro logístico está estratégicamente localizado dentro de un círculo de 3 km de radio en el que se encuentran cuatro de sus principales fábricas y a menos de 100 km de distancia de otras tres, lo cual facilita y agiliza el transporte de la carga entre las fábricas y el centro logístico.
El flujo de movimientos es muy intenso y continuo, por eso se han colocado dos muelles de recepción en un lateral del depósito, apartado de los nueve muelles de expedición para no interferir entre las dos operativas, con un amplio espacio que permite un movimiento más dinámico de las maniobras de transporte y la espera de los camiones.
El edificio anexo al depósito está constituido por dos plantas diferentes con el fin de organizar óptimamente las diferentes operativas que se realizan:
- La planta inferior está destinada principalmente a la recepción y a la expedición de la mercadería, con una amplia zona de precargas en el suelo.
- En la planta superior, los pallets procedentes de los muelles del nivel inferior, entran dentro del depósito. También hay un área dedicada a las tareas de picking.
El depósito
El depósito dispone de unas dimensiones considerables: 102 m de largo, 57 m de ancho y 35,5 m de altura, el máximo admitido por las normativas locales. Está distribuido en ocho pasillos con estanterías de doble fondo a ambos lados, cada una con 14 niveles de carga de distintas alturas adaptadas a los formatos de pallets de Grupo Siro: cinco niveles para europallets de 1.400 mm de alto, ocho de 2.000 mm y uno de 2.500 mm. Las unidades de carga tienen un peso medio de 800 kg y un máximo de 1.000 kg.
Cada pasillo está equipado con un transelevador bicolumna con horquillas telescópicas y una cabina de mantenimiento embarcada en la cuna. Esta máquina se encarga de almacenar cada pallet en su ubicación correspondiente en función de su tamaño y su rotación.
La automatización del depósito se completa con dos circuitos de transportadores: uno en la planta baja donde se depositan los pallets destinados a las expediciones, y otro en la planta superior, a 6,7 m de altura, que conecta todas las entradas además de las salidas a la zona de picking.
En la parte superior del depósito se han aprovechado los espacios libres entre las cerchas para ubicar los conductos de aire acondicionado que regulan la temperatura de toda la instalación y distribuyen correctamente el aire.
En el exterior del edificio, en la parte posterior, se han habilitado cuatro equipos de bombeo del sistema contraincendios y un depósito de agua con suficiente capacidad para las dimensiones del mismo. En el interior se encuentran los rociadores y detectores que evitan cualquier conato de incendio.
La planta baja
Distribución de la planta baja:
- Muelle de descarga automática
- Muelle de descarga convencional
- Muelles de carga (9 en total)
- Zona de control de entrada de pallets y elevador
- Salidas de pallets desde el depósito
- Precargas en el suelo
- Circuito virtual de autoelevadores LGV
- Acúmulo de pallets vacíos
- Recepción y acondicionamiento de pallets de entrada
Entrada de mercadería
La entrada de las mercaderías procedentes de los distintos centros de producción más cercanos se llevan a cabo desde los dos muelles de recepción, uno de ellos con descarga automática de los camiones y el otro manual utilizando autoelevadores o transpallets.
El área de descarga tiene una capacidad de acúmulo de dos camiones completos, es decir, un total de 66 pallets que se dirigen a la zona de inspección donde se valida su estado.
Todos los pallets pasan obligatoriamente por el área de inspección, donde se verifica que estén en buen estado y que su peso y sus medidas se correspondan con los requisitos de calidad exigidos en el depósito.
Si el pallet es correcto, el sistema de control da la orden para que siga su camino hasta el elevador, que lo trasladará a la planta superior, y entonces entrará en el depósito automático.
Cuando el pallet no supera el control, puede dirigirse a tres zonas diferentes, dependiendo de la anomalía detectada:
- La zona de reacondicionamiento.
- El área de compactación, donde se corrigen los desplomes que sobrepasen los límites previstos.
- El remontado de pallets: cuando las unidades de carga disponen de una base inadecuada se colocan encima de otra en buen estado mediante los remontadores. Estos pallets regresan al área de inspección y son verificados de nuevo antes de acceder a la planta superior.
El pallet defectuoso que no tiene ninguna posibilidad de corregirse, se transportará hasta la zona de salida y se expulsará del circuito.
Los pallets que han sido reacondicionados vuelven a cruzar el puesto de inspección para comprobar de nuevo que cumplen con los requisitos del depósito.
Es necesario garantizar que la mercadería que se introducen en el depósito automático sea la adecuada y se debe comprobar que la carga no desborde más de lo previsto.
Salidas del depósito / Expediciones
Los autoelevadores de guiado automático (LGV) manipulan los pallets que salen del depósito, recogiéndolos en los puntos de salida de cada pasillo de almacenaje y transportándolos hacia la zona de espera asignada en alguno de los nueve muelles de carga, siguiendo un circuito virtual previamente programado.
El autoelevador define su trayectoria al emitir una señal láser que rebota en deflectores colocados en puntos cercanos al recorrido. El sistema de gestión puede conocer con exactitud su posición y da la orden de dirigirse a las estaciones de recarga cuando el nivel de baterías llega a un límite establecido. Al ser una conexión totalmente automática, no es necesaria la intervención humana en este proceso.
Solo la carga de los camiones la realizan los operarios, que ayudados por transpallets introducen la mercadería en el camión asignado por el sistema de gestión de depósitos en función del número de pedido, la ruta a efectuar, el cliente, etc.
El personal confirma cada operación y cumplimiento de las órdenes mediante un terminal de radiofrecuencia.
La planta superior
Organización de la planta superior:
- Elevador
- Circuito interno del depósito
- Transportadores de entrada o salida de cada pasillo
- Lanzadera de la zona de picking
- Puestos de picking
- Zona de enfardado y reacondicionamiento
- Transportador principal de entrada al depósito
Entrada al depósito
La mercadería procedente de los muelles de recepción, una vez ha superado el área de inspección, accede a la primera planta a través del elevador.
Entonces un transportador principal distribuye las referencias por los transportadores de entrada a los diferentes pasillos de almacenaje. Es un circuito de una sola dirección por el que también se desplazan los pallets que salen de los pasillos y se dirigen a las zonas de picking.
Zona de picking
Asimismo, se han instalado dos puestos de picking unidos en los que cada operario puede preparar dos pedidos a la vez. La zona está preparada para ser ampliada en un futuro si las necesidades de Grupo Siro así lo requieren.
Los puestos de picking están colocados encima de transportadores. A ambos lados del operario se encuentran las mesas de elevación hidráulicas que se ajustan a una posición ergonómica para manipular la mercadería. De este modo, la preparación de pedidos es mucho más ágil.
Cada puesto de picking dispone de un circuito de acúmulo. También se han habilitado apiladores y dosificadores de pallets que abastecen el área, así como estaciones de espera de pallets que han salido del depósito y no tienen un hueco libre en el circuito del puesto asignado.
Una vez finalizado el pedido, el pallet se incorpora al circuito de transportadores que, después de pasar por la enfardadora, lo trasladará de nuevo al depósito hasta que el sistema de gestión ordene su expedición.
El software
El depósito está gestionado mediante el software Easy WMS de Mecalux y se comunica constantemente con el sistema de planificación de recursos de Grupo Siro, con la intención de controlar, coordinar e informar de todos los procesos logísticos y las operativas que se desarrollan dentro del depósito.
El software está concebido para tener un carácter práctico y operativo, además de realizar estas funciones:
- Control absoluto sobre la gestión del depósito.
- Gestión de la entrada y salida de la mercadería desde los muelles de carga y descarga.
- Colocación estratégica de las unidades de carga en el depósito siguiendo un control de los pasillos y sus ubicaciones.
- Registro y ajuste del stock en tiempo real.
- Diseño del orden de salida de la mercadería y su posterior carga en el camión mediante un terminal de radiofrecuencia.
- Optimización de las tareas según el recorrido de picking.
- Comunicación directa con el proveedor logístico de Grupo Siro.
- Coordinación de todos los datos maestros (artículos, propietarios, proveedores, clientes, etc.).
Beneficios para Grupo Siro
- Ahorro en los costes operativos: la eliminación de los depósitos externos y la centralización de las operaciones en el mismo centro logístico repercute en un aumento de la productividad y en un rápido retorno sobre la inversión.
- Máxima capacidad: la gran altura del depósito y el uso de transelevadores ha permitido multiplicar la capacidad de almacenaje de Grupo Siro, adecuándose al crecimiento de su producción.
- Gestión totalmente automatizada: Grupo Siro ha integrado y coordinado sus operativas de recepción, almacenaje, picking y expedición de mercaderías en un solo espacio, bajo la gestión y el control de Easy WMS, optimizando el rendimiento de toda su cadena logística.
- Incremento de la seguridad: los depósitos automáticos ofrecen la máxima protección para los operarios y la mercadería, contribuyendo de este modo al objetivo de la empresa de fomentar procesos eficientes que garanticen en todo momento la seguridad de las personas.
Cámara de congelación en Mar del Plata (Buenos Aires - Argentina) | |
---|---|
Longitud: | 16.200 mm |
Anchura: | 24.850 mm |
Altura: | 11.700 mm |
Nº de estanterías con Pallet Shuttle: | 4 bloques de 9 m de altura y diversas medidas de longitud y profundidad |
Nº de Pallet Shuttle: | 2 carros eléctricos |
Nº niveles de carga: | 5 |
Nº pasillos: | 1 |
Anchura de pasillo: | 3.200 mm |
Unidad de carga: | Pallets Arlog, 1.000 x 1.200 mm, con 1.700 mm de altura y 1.000 kg de peso |
Capacidad total del depósito: | 650 pallets |
Galería
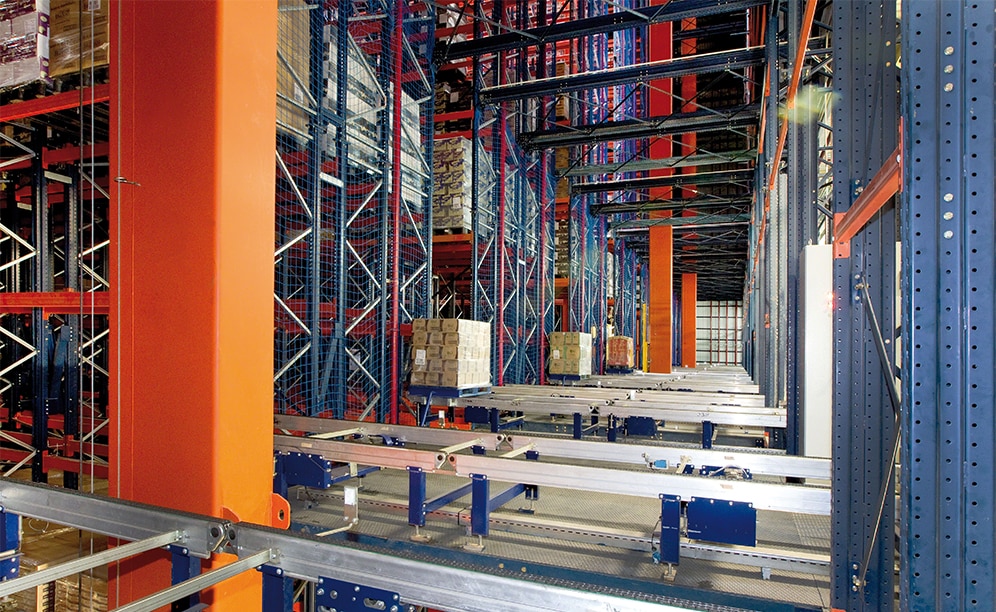
Mecalux ha construido un depósito autoportante de grandes dimensiones completamente automatizado para Grupo Siro
Consulte con un experto