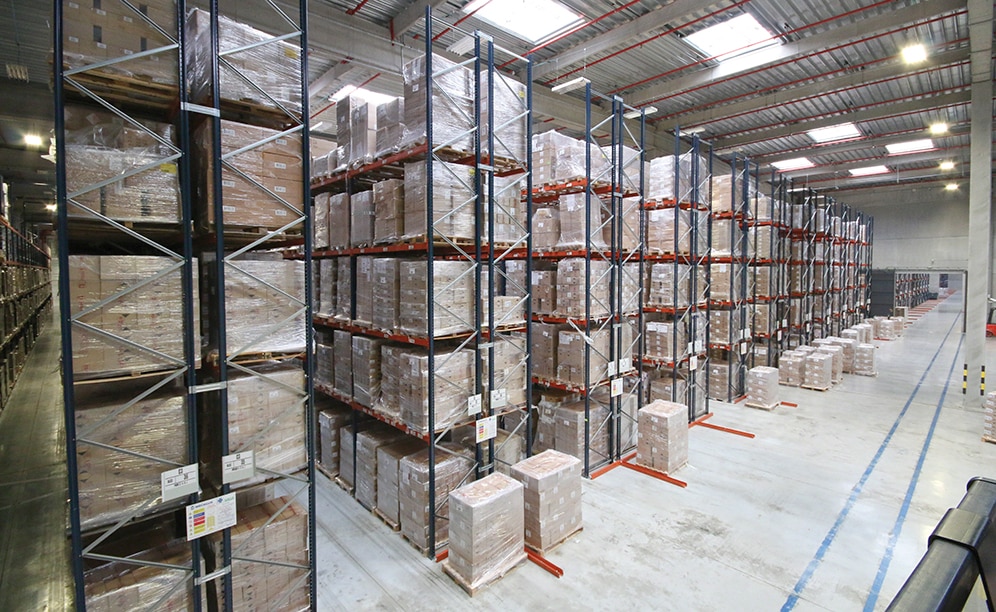
Depósito sectorizado para más de 42.000 pallets y una zona de picking para la empresa SAGA
Un completo circuito de picking para el depósito de SAGA en Francia
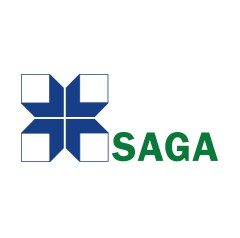
Con una capacidad total que supera los 42.000 pallets, en el depósito que SAGA posee en Saint-Priest cobra un gran protagonismo el área específica de picking, ya que la empresa precisa una gran agilidad para atender las demandas de su red de oficinas presente en más de 100 países. Esta zona de picking, formada por racks selectivos, satisface todas las necesidades de SAGA a la vez que reduce los costes de explotación.
Un depósito dividido
El depósito de SAGA está sectorizado en cinco módulos independientes que quedan aislados entre ellos como medida de prevención de incendios. En cada uno de ellos, se han dispuesto racks selectivos, pero con la diferencia de que los módulos 1, 2 y 3 están servidos por autoelevadores de tipo trilateral, mientras que en los otros dos se trabaja con autoelevaores retráctiles.
Además, en estos dos últimos módulos se almacena la reserva de los productos que se preparan en el área específica de picking, instalada en el módulo 5.
Puesto que las máquinas trilaterales trabajan únicamente en el interior de los pasillos de almacenaje, otros autoelevadores, en especial los transpallets, se encargan de depositar y recoger los pallets de los extremos de los pasillos. Para que puedan dejarlos centrados, los racks cuentan con posicionadores anclados en el suelo.
Estos elementos no son necesarios en los racks servidos con autoelevadores retráctiles, pero sí que se han colocado protecciones en los puntales y laterales para prevenir posibles impactos, tal y como se observa en la fotografía de la derecha.
Zona de picking: proceso a seguir para la preparación de los pedidos
1.- La conformadora automática de cajas crea cajas del tamaño que se necesite a partir de cartón plano de distintos formatos.
2.- Las cajas conformadas se acumulan en un circuito en forma de “U” y van entrando en el circuito principal a medida que se precisan. Posteriormente, se adhiere de forma automática una etiqueta de identificación.
3.- Las estanterías para picking dinámico, ubicadas en el inicio del circuito, están dispuestas a ambos lados de los dos pasillos, permitiendo almacenar más de un centenar de referencias de tipo A repartidas en 48 módulos. Debajo de una de las estanterías de picking y entre dos niveles de almacenaje, circula el transportador continuo para los pedidos ya finalizados. Junto a éste, se encuentra el otro transportador no automatizado que cumple la función de mesa de preparación.
4 y 5.- El circuito de transportadores recorre los dos pasillos anteriores. Uno de los módulos es basculante, posibilitando el paso de personas y carros a la siguiente zona.
6.- En esta segunda zona se preparan los productos de tipo B y C. Para ello, se han habilitado 36 módulos de estanterías dinámicas y 112 módulos dobles de racks selectivos.
7.- Los pedidos, una vez se han preparado, son conducidos hasta el puesto de verificación y control de peso, donde se comprueba que no haya errores y que el pedido esté completo.
8.- En el área de embalaje se colocan y protegen los productos antes de pasar por las distintas máquinas que cierran y precintan las cajas. A continuación, se imprimen los albaranes para ser introducidos en las cajas y se adhieren manualmente el resto de etiquetas que se requieren para su expedición.
9.- Esta zona cuenta con 12 canales de clasificación automática de pedidos, que corresponden a rutas diferentes.
La zona de picking se compone de las siguientes partes:
- Conformadora de cajas de cartón.
- Transportadores de identificación y acúmulo de cajas vacías.
- Estanterías dinámicas para cajas (destinadas a productos de alta rotación) combinadas con transportadores.
- Transportadores de cajas.
- Módulo basculante para permitir el paso entre zonas.
- Zona de estanterías dinámicas para productos de media rotación (tipo B) y convencionales para productos de baja rotación (tipo C).
- Verificación de pedidos preparados Zona de embalado, emisión de albaranes, etiquetado y precintado.
- Zona de clasificación de pedidos.
Preparación de pedidos
Cada vez que se lanza un nuevo pedido, el SGA (Sistema de Gestión de Depósitos) indica al acumulador de cajas la cantidad y el tamaño de cajas necesario.
Posteriormente, la etiquetadora automática adhiere a la caja las etiquetas con su respectivo código de barras. El operario coge la caja y lee su código mediante el terminal de radiofrecuencia para que el sistema le indique qué mercadería precisa y cuánta cantidad debe coger.
El depósito está dividido en varias zonas y en cada una de ellas hay asignado un operario. Cuando el primer operario ya ha preparado la parte que le corresponde, traspasa la caja al siguiente para que continúe el proceso. Según se van finalizando los pedidos o se van llenando las cajas, se introducen en el transportador automático que pasa por el interior de los racks.
Aunque el circuito continuo tiene forma de “U”, aquellas cajas que necesiten productos de media y baja rotación se desvían a un transportador de acúmulo a la espera de que el operario asignado a esta zona empiece a preparar esas referencias.
El operario de la zona B y C utiliza un carro que admite seis cajas de seis pedidos diferentes.
El proceso termina con el traspaso manual de estas cajas a los pallets correspondientes y su posterior expedición.
La gran capacidad del depósito, su sectorización y especialización, así como la ubicación de los muelles de carga y la flexibilidad obtenida con los sistemas de almacenaje y picking instalados, permiten a SAGA ofrecer un servicio eficaz y ágil a sus clientes.
Beneficios para SAGA
- Alta capacidad de almacenaje: el depósito de SAGA está capacitado para almacenar más de 42.000 pallets en una superficie de 48.000 m2.
- Aumento de la velocidad en la preparación de pedidos: un eficiente circuito de picking optimizan los movimientos durante la preparación de pedidos de alta, media y baja rotación.
- Reducción de los costes: cada sector dispone de sus propios muelles de carga, evitando así grandes desplazamientos y reduciendo notablemente los costes de explotación.
Racks selectivos | |
---|---|
Capacidad de almacenaje: | 42.410 pallets |
Peso máximo por pallet: | 800 kg |
Tamaño del pallet: | 800 x 1.200 mm |
Altura del depósito: | 9 m |
Galería
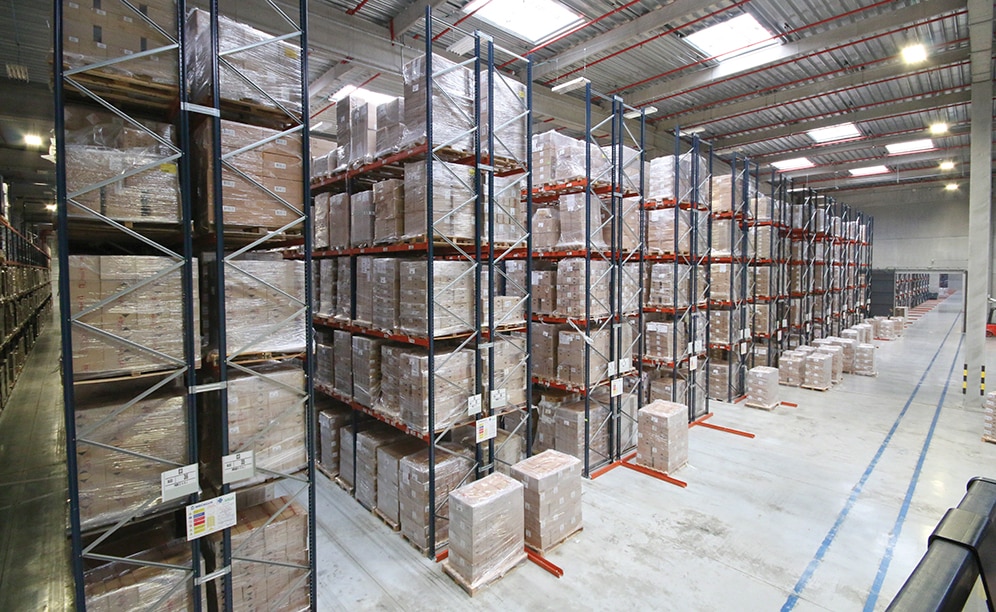
El depósito de SAGA está capacitado para almacenar más de 42.000 pallets
Consulte con un experto