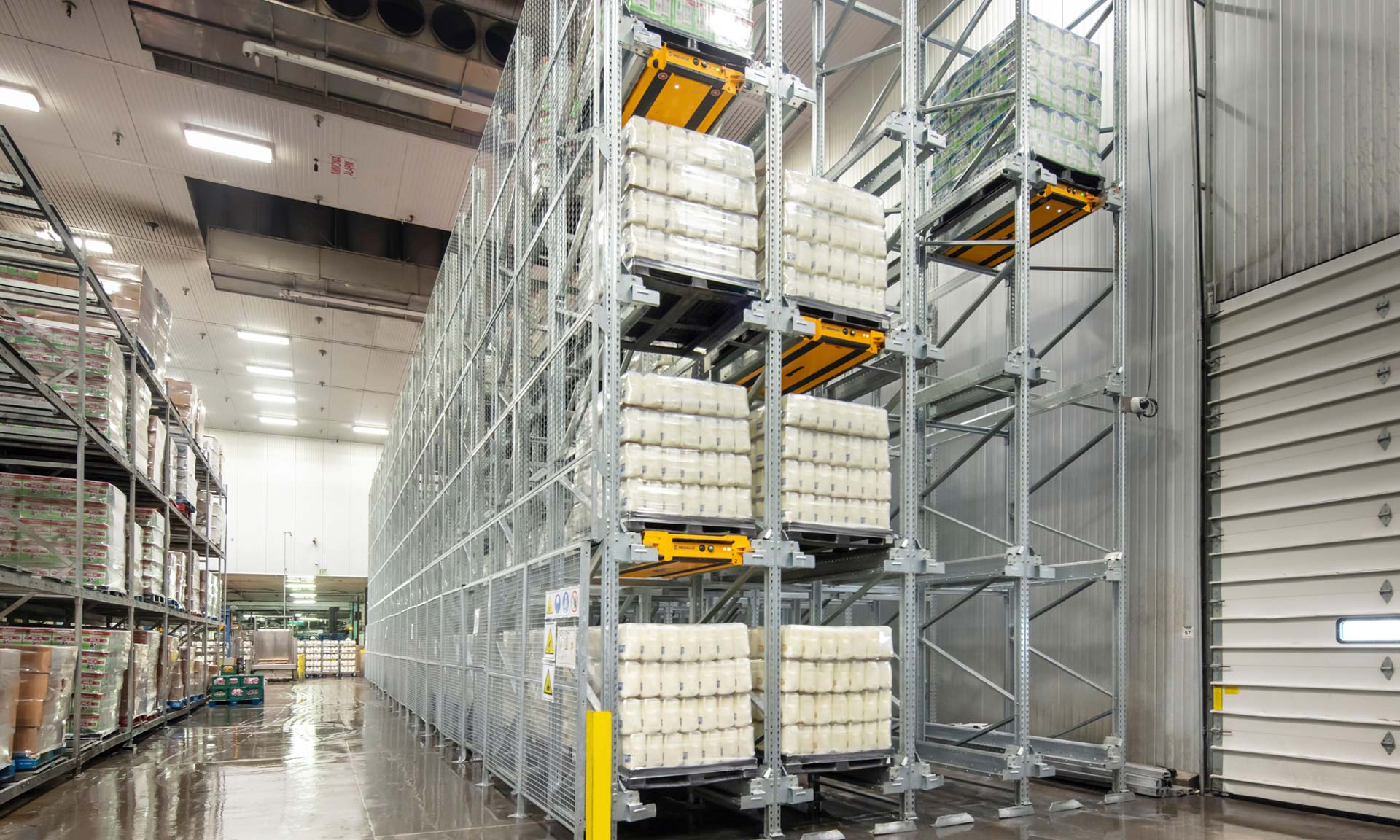
El Pallet Shuttle duplica la capacidad
Producers Dairy ha duplicado la capacidad de almacenamiento con el sistema Pallet Shuttle de Interlake Mecalux
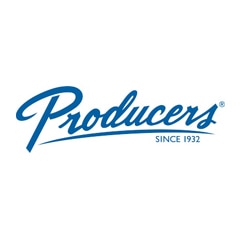
El proveedor y distribuidor de productos lácteos Producers Dairy ha equipado su cámara de refrigeración de 4.645 m² en la planta de producción que posee en Fresno (California) con el sistema Pallet Shuttle semiautomático de Interlake Mecalux. La firma ha sustituido sus anteriores racks que se habían quedado obsoletas con el sistema Pallet Shuttle. Con esta solución, la compañía ha duplicado la capacidad de almacenamiento y puede preparar hasta 300 pedidos al día.
Alimentando vidas
Durante los años treinta del siglo pasado, la Gran Depresión obligó a muchos norteamericanos a viajar a California en busca de oportunidades y trabajo. Por aquel entonces, cuatro ambiciosos empresarios fundaron Producers Diary Inc. En la primavera de 1949, Larry Shehadey adquirió una participación mayoritaria en la empresa que sigue funcionando hoy en día como un negocio familiar. En la actualidad, la firma posee dos plantas de producción en California, una en Nevada y otra en Oregón. La planta de producción de mayores dimensiones, de 12.541 m², se encuentra en Fresno, California, donde se embotellan todo tipo de productos lácteos como leche y helados, así como zumos de naranja o manzana.
Nuevo sistema de almacenamiento de pallets
Dada la antigüedad de los racks existentes, la empresa era consciente de que necesitaba encontrar un nuevo sistema de almacenamiento para su cámara de refrigeración de 4.645 m² en sus instalaciones de Fresno. “Los racks eran cada vez menos operativas, por lo que estábamos buscando un sistema de almacenamiento más eficaz para sustituirlas”, afirma Mike Ramirez, director de la planta de Producers Dairy.
La situación era tan crítica que la compañía estaba perdiendo capacidad de almacenamiento a pasos forzados: “Llegamos al punto de tener que dejar de utilizar los dos niveles superiores de los racks. Como consecuencia, nos quedamos con tan solo 180 ubicaciones donde almacenar los pallets”, añade Ramirez.
Fue entonces cuando Interlake Mecalux y su socio PacVS intervinieron. “Nos propusieron el sistema Pallet Shuttle de Interlake Mecalux, una solución que se ajustaba totalmente a nuestra operativa”, afirma Ramirez. Este sistema de almacenamiento por compactación emplea un carro con un motor eléctrico que se desplaza por el interior de los canales de almacenamiento. Mediante el carro, la compañía ha acortado considerablemente los tiempos de entrada y salida de la mercadería. Asimismo, con este sistema de almacenamiento los operarios pueden agrupar las 150 referencias de forma correcta (cada canal corresponde a un artículo diferente).
El sistema Pallet Shuttle también resolvió los problemas de capacidad de almacenamiento de Producers Dairy, al poder alojar 370 pallets (más del doble que los 180 almacenados antes). Los racks miden 7 m de altura, con cuatro niveles, y disponen de cinco carros motorizados encargados de almacenar los pallets americanos (1.000 x 1.200 mm) con los que trabaja la compañía.
Los carros motorizados siguen las instrucciones que les envían los operarios a través de una tablet con conexión wifi especialmente diseñada para trabajar a bajas temperaturas (la cámara de refrigeración de Producers Dairy opera a 4 ºC). El sistema Pallet Shuttle es una solución perfecta para gestionar productos que necesitan almacenarse a bajas temperaturas, porque aprovecha la superficie de almacenamiento y reduce el tiempo necesario para manipular la mercadería.
Al prescindir de autoelevadores circulando por el interior de las calles de almacenamiento, aumenta la capacidad de almacenamiento (los racks pueden ser más profundos) y disminuye el riesgo de posibles accidentes.
El operario, con un autoelevador, sitúa el carro motorizado en el canal donde va a almacenarse el pallet. A continuación, deposita el pallet en la entrada de ese canal, apoyándolo en los carriles (solo las horquillas del autoelevador penetran en la estructura de los racks para introducir o extraer la mercadería). Después, el carro motorizado levanta ligeramente el pallet y lo desplaza horizontalmente por el canal hasta llegar a la ubicación más profunda disponible. Es entonces cuando el carro motorizado regresa a la entrada del canal para repetir el mismo movimiento con el siguiente pallet. Esta secuencia se repite las veces necesarias hasta completar el canal. Antes de llenar la última posición del canal, el operario retira el carro eléctrico y repite la secuencia en el siguiente canal donde sea preciso trabajar.
El sistema Pallet Shuttle es una solución ideal para empresas con un gran número de pallets por referencia y una alta rotación de mercaderías (con entradas y salidas masivas de un mismo producto). Producers Dairy se sirve de este sistema de almacenamiento en su cámara frigorífica para almacenar los productos durante un periodo de tiempo muy breve. “En nuestra planta embotellamos los productos lácteos procesados. Se agrupan encima de un pallet y se almacenan en los racks con el Pallet Shuttle durante 24 horas aproximadamente”, asegura Ramirez. “Luego, se introducen en un camión y se entregan a los clientes”. La empresa carga entre 50 y 70 camiones al día con unos tres o cuatro pedidos en cada uno de ellos (en total, se reparten unos 300 pedidos al día).
Problemas adicionales resueltos
Además de solucionar la falta de capacidad en la cámara frigorífica de Producers Dairy, el sistema Pallet Shuttle de Interlake Mecalux también ha proporcionado más ventajas. Por una parte, ha rebajado los costos de servicio de la empresa al lograr un importante ahorro del consumo energético para generar frío (el frío se distribuye entre un mayor número de pallets almacenados). Por otra, el carro motorizado está dotado de baterías de litio que pueden trabajar en un rango muy amplio de temperaturas sin que se degrade o se acorte su vida útil.
El sistema Pallet Shuttle también puede acumular una gran cantidad de mercadería, por lo que la compañía dispone de productos para abastecer a sus clientes en caso de que la planta tenga que interrumpir una línea de producción para realizar tareas de mantenimiento. “Si sufrimos alguna incidencia imprevista que interrumpa nuestra producción, disponemos de la mercadería necesaria, debidamente organizada, para seguir operando”, comenta Ramirez. “Antes no podíamos hacerlo y esta es, probablemente, una de las mejoras más positivas para nuestro negocio”.
Planes de expansión
El proyecto ha tenido tanto éxito que Producers Dairy tiene previsto ampliar los racks con Pallet Shuttle en un futuro. “Nuestro espacio es muy limitado, así que tuvimos que instalar las nuevos racks tomando como base las dimensiones de los racks antiguos”, señala Ramirez. “Nos gustaría aparte ensanchar la cámara frigorífica. Para ello, derribaremos la pared adyacente a los racks y ganaremos espacio que destinaremos a ampliar la capacidad de almacenamiento”.
Si sufrimos alguna incidencia imprevista que interrumpa nuestra producción, disponemos de la mercadería necesaria, debidamente organizada, para seguir operando. Antes no podíamos hacerlo y esta es, probablemente, una de las mejoras más positivas para nuestro negocio.
Ventajas para Producers Dairy
- Doble capacidad de almacenamiento: al sustituir los racks de paletización por el sistema Pallet Shuttle semiautomático, Producers Dairy ha pasado de almacenar 180 pallets a dar cabida a 360 en el mismo espacio.
- Ahorro de energía: los racks con Pallet Shuttle ayudan a reducir notablemente el consumo de energía para generar frío.
- Mayor flexibilidad: Producers Dairy dispone de mercadería almacenada para suministrarla a sus clientes sin interrupción, incluso en el supuesto de detener alguna línea de producción para realizar labores de mantenimiento.
Galería
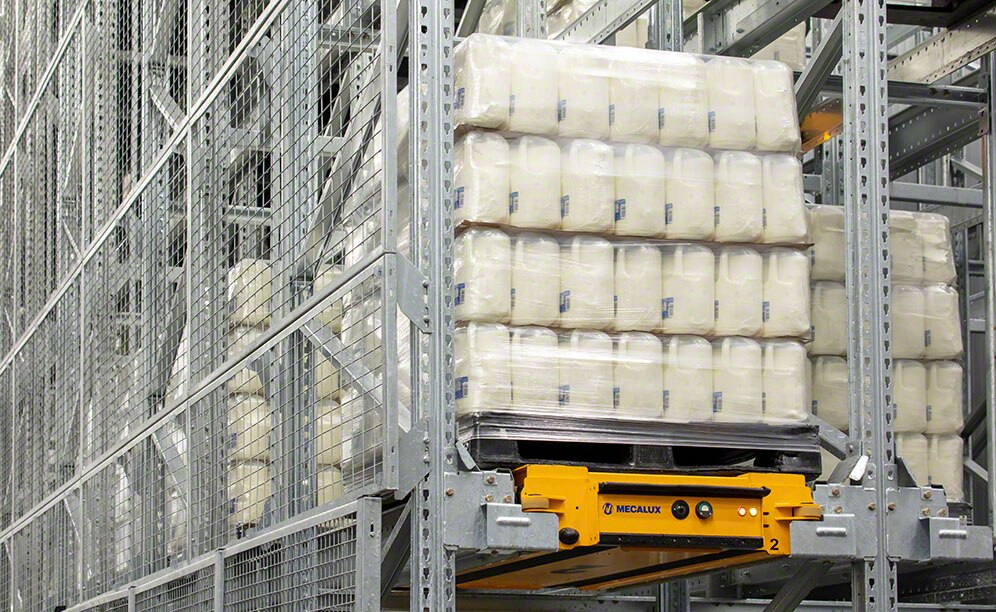
Producers Dairy ha renovado su depósito con el sistema Pallet Shuttle
Consulte con un experto